


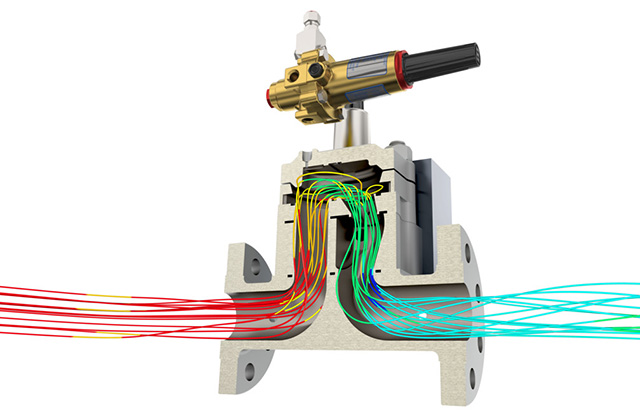
To break the link and move conditions to the main assembly’s project, right-mouse click on a condition in the Stored in Model tree and select Move to Project. Once imported, conditions appear in the Stored in Model tree in the linked mode so that they are linked to the conditions in the component. To use conditions from a component (part of assembly), open the Import from Model dialog and select the project you want to use data from. However, you can break the link so imported conditions are not linked to the original component. In that case instead of creating conditions for all PCBs again inside the assembly a few times, you just link the assembly’s project to the conditions defined in the PCB.īy default conditions are linked, so changing conditions in the component automatically updates conditions in the assembly.
#Solidworks flow simulation 2016 full
If the model is used in an assembly, you can use conditions defined in this low-level component for the higher-level assembly without recreating this condition again.įor example, you analyze a PCB first and then you want to analyze the full electronics enclosure with the few PCBs installed. How does this work in SOLIDWORKS Flow Simulation 2017?įirst, a Flow Simulation project is saved in directly inside of your SOLIDWORKS model. Conditions from Low-Level Component: Import Condition in Model: The ability to import from model conditions defined for other projects (such as material properties, heat power etc.) can dramatically simplify project definition by creating a library of models with pre-defined conditions.This blog post will introduce you to four new features including: import condition in model, multi-parameter optimization, transient simulation performance, instant switching between transient time moments. The insight gained from these computational fluid dynamic (CFD) studies provide insight that can help you pinpoint problems earlier so you can fix problems faster and at less cost. The instructor spent time after class one-on-one with him and covered many topics to solve most of the issues.The newest release of SOLIDWORKS Flow Simulation 2017 is packed with new user-requested enhancements that make it even easier and faster to determine the impact of a liquid or gas flow on your product designs during the design phase-long before physical protoypes are created. One of our training instructors received rave reviews from a self-taught Simulation customer who was becoming fed up with issues in one of his studies.We were able to help them save money in the long run, narrowing down the design to two iterations for prototyping after predicting issues with other designs. After consulting with the Hawk Ridge team, they moved forward with Simulation. One customer was worried about the costs for shaker table testing prototypes of multiple design iterations.Our simulation team was able to help them understand the problem and coach them through a better approach, scaling back to start simple and build from there. We worked with a customer encountering mesh issues and failed studies on a complicated model.We take pride in having in-depth conversations with customers like you to understand your short and long-term goals so that we can provide honest feedback and recommendations. We are with you every step of the way from initial interest to working with you on your first analysis project and beyond. Our simulation technical team is full of degreed engineers who have multi-disciplinary experience across different industries. The Hawk Ridge team is here to help you succeed.
